What Does AQL? How to Read AQL Table?
Acceptance Quality Limit or AQL for short, is a statistical method used to inspect a certain sample size for a given lot and set the maximum number of acceptable faults. It is defined as a "quality level that's worst tolerance in standard ISO 2859-1."
Stated differently, it represents the worst process average that can be tolerated when a continuous series of lots are submitted for acceptance sampling. Typically, one for each of the three limits—critical, major, and minor—is selected. Typically, every category has a particular set of these three limitations, which are well-known to the majority of Asian exporters. AQL, formerly known as "acceptance quality level," is a crucial metric for businesses aiming to achieve Six Sigma-level quality control. While a product's AQL would differ depending on the industry, Businesses that deal with medical devices or extreme sports equipment would need to adhere to stricter AQL standards because accepting faulty products could pose health hazards.
Keywords: AQL Table/ANSI AQL Chart:
The standard definition of Acceptance Quality Limit (AQL) is “the maximum defective percent (or the maximum number of defects per hundred units) that, for purpose of sampling inspection, can be considered satisfactory as a process average”.
Keywords: Three Types Of Defects For Consumer Goods:
Critical Defects: Totally unacceptable defects, when accepted could lead to harm to the users. or regulations are not respected. It is defined by ZERO (AQL Table c=0)
Major Defects: Defects are usually not acceptable by the end-users, the AQL for a major defect is 1.5 or 2.5 (AQL 1.5 or AQL 2.5)
Minor Defects: Defects, which are not likely to reduce materially the usability of the product for its intended purpose but slightly differ from specified standards. most end users won’t mind it. The AQL for minor defects is 4.0
Keywords: Lot Size In AQL Chart
The quantity of each product is the lot size, if you ordered different products, then each product considers a separate lot.
Keywords: General Inspection Level (G-I, G-II, G-III)
Different inspection levels will command different numbers of samples to inspect. General Level II in single sampling plans is the normally used sampling method.
Keywords: Special Inspection Level (S-1, S-2, S-3, S-4)
The special levels can be applied in cases where only a few samples should be checked, mostly the special levels are used only for certain on-site testings, and spot check during container loading supervision.
Keywords: AQL 2.5
When a product defect adversely affects the performance of the product or varies significantly from the specifications, or the defects cause the end customer to return the product, the inspector will the defects to be a “Major”, and the most common AQL inspection assigned to Major defects is 2.5.
Keywords: AQL 4.0
Typically, minor defects are relatively small or insignificant issues, these issues won’t affect the product’s functionality or form, and customers won’t return the product based on the presence of one or very few minor defects on the product. but AQL 4.0 is typical for the acceptance of minor defects, your goods may fail inspection if the number of minor defects found beyond AQL 4.0
Keywords: Inspection Standard ASQ Z1.4 / ISO 2589-1
ANSI/ASQ Z1.4-2003 (R2013): Sampling Procedures and Tables for Inspection by Attributes is an acceptance sampling system to be used with switching rules on a continuing stream of lots for the Acceptance Quality Limit (AQL) specified. ISO 2859-1:1999: Sampling procedures for inspection by attributes — Part 1: Sampling schemes indexed by acceptance quality limit (AQL) for lot-by-lot inspection It provides tightened, normal, and reduced plans to be applied for attributes inspection for percent nonconforming or nonconformities per 100 units.
How to use the AQL Table?
A: Determine The Sample Size By Using AQL Table
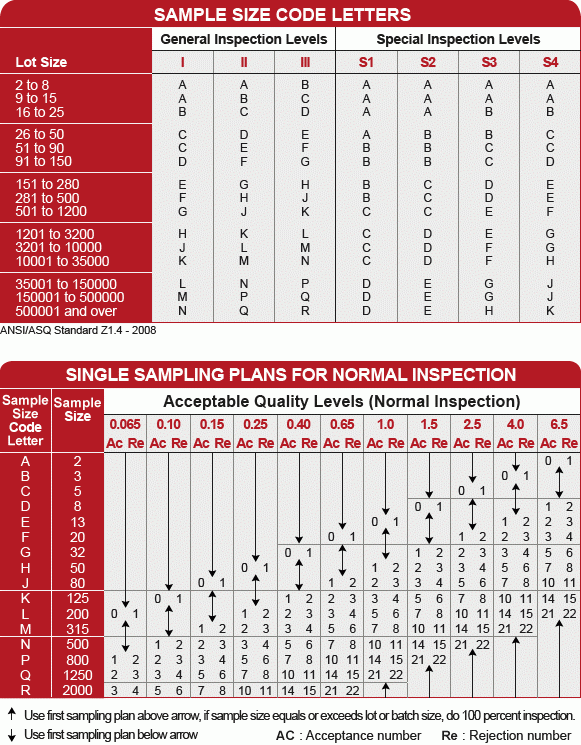
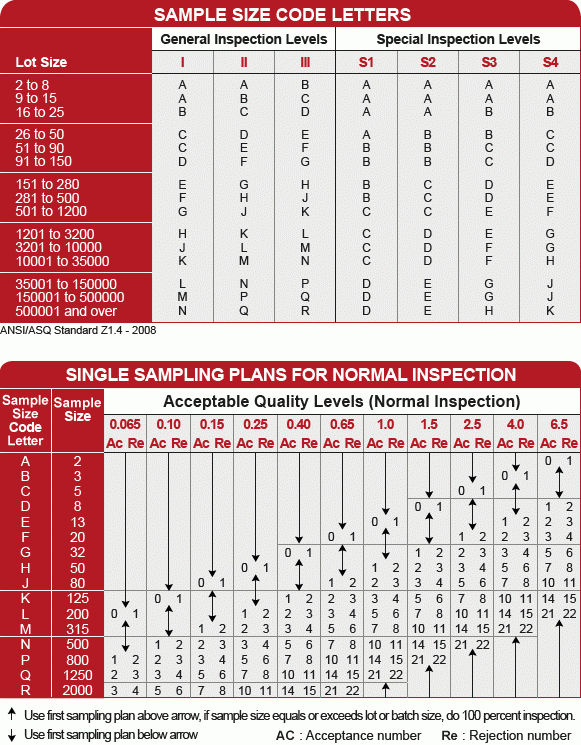
The AQL table will help you to determine the sampling size, we will need to inspect it according to your ordered quantity and your level of severity (G-I, II, or III). And the standard level, the one used by default and by 98% of buyers is the General level G-II for a standard AQL inspection. If your order has multiple references, ideally we should at least inspect a level II on each reference. Indeed, for a standard order, the standard level II from the AQL table gives the minimum sampling size we should check per reference if we do not want to take additional risks. If we inspect a G-II sampling size on multiple reference orders, then the AQL sampling size is diluted and divided by the number of references, increasing the risks as the sampling size must be representative enough. In order to find the necessary sampling size to be inspected, we look at the first chart and find on the left side the range of items being produced in total. You have the choice of levels I, II, and III, with Level III being the most stringent testing and level I being the least. As we said above, Level II is the standard and is most often used. For example, if you are producing 8000 items, at AQL Chart level II you have the letter L, which in the second table says to inspect 200 items.

B: Define The Acceptable Quality Limit
Usually, most importers will choose standard defect levels which are 0/2.5/4.0 but one can choose 1/1/1 if he wishes or 0/1.5/2.5 like in the automotive industry. Using the standard 0/2.5/4.0 defect levels and a sample size of 200, we see that if you have more than 0 critical defects, 10 major defects, or 14 minor defects, you should reject your shipment. Of course, the decision about what to do after you received the inspection reports belongs to you, inspection only can give suggestions. So most importers will put AQL sampling into the purchase contract and inspection checklist to avoid any misunderstanding in production, suppliers will be clear with your quality requirements. Importers will also wish to discuss all inspection findings with their vendor/manufacturer in order to improve whatever possible. In case the inspection results are very close to AQL limits, it is vital that you double-check if the AQL of found defects is acceptable to you or not. Check the below chart of defect findings to better understand the acceptable quality limits.
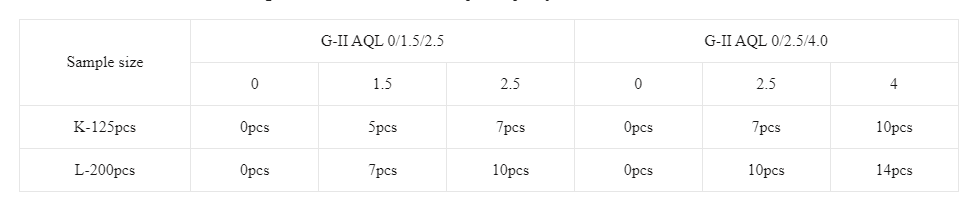